Mold Tooling: Essential Insights for Metal Fabricators
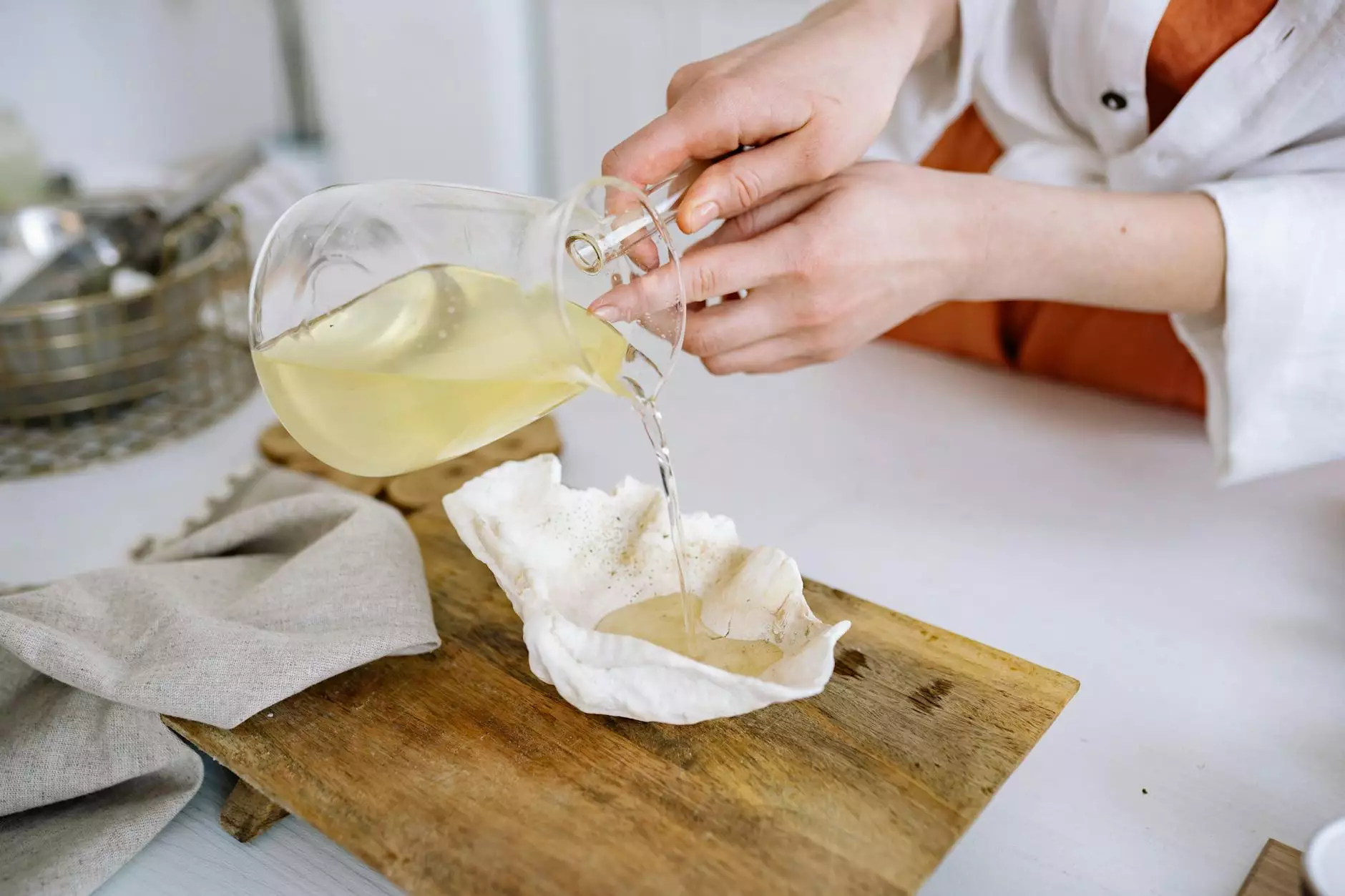
In the dynamic landscape of metal fabrication, the role of mold tooling cannot be overstated. It is a proprietary process that forms the backbone of manufacturing various metal components required in diverse industries. Understanding mold tooling can significantly enhance productivity, reduce costs, and improve the quality of finished products. In this comprehensive article, we will delve into the intricacies of mold tooling and its significance within the realm of metal fabrication.
What is Mold Tooling?
Mold tooling refers to the engineering process of creating molds that form products from heated materials. These molds are usually made from metals, plastics, or rubber, and are utilized in processes such as injection molding, compression molding, and blow molding. It's a critical step in the production of high-quality components with precision tolerances.
The Importance of Mold Tooling in Metal Fabrication
Mold tooling plays a pivotal role in ensuring that metal fabricators achieve their production goals efficiently. Here are some of the key reasons why mold tooling is vital:
- Precision Engineering: Mold tooling allows for the creation of highly accurate products. Thanks to the meticulous design and manufacturing processes, mold tooling can ensure that the parts produced meet exact specifications.
- Cost-Effectiveness: Effective mold tooling can significantly reduce production costs. High-quality molds help minimize material wastage and speed up production times, leading to increased profitability.
- Versatility: Mold tooling can be adapted for various materials and types of fabrication processes, making it suitable for a range of applications across different sectors, including automotive, aerospace, and consumer goods.
- Rapid Prototyping: With the advancement of 3D printing technologies, mold tooling has transitioned into rapid prototyping, allowing manufacturers to receive prototype molds swiftly for testing and feedback.
The Mold Tooling Process
The mold tooling process can be broken down into several crucial stages, each contributing to the efficacy and quality of the final product. Here is a more detailed look at these stages:
1. Design Phase
The first step in the mold tooling process involves designing the mold itself. This often entails collaborating with engineers and product designers to develop a design that meets the functional and aesthetic requirements of the final product. Utilizing advanced CAD (Computer-Aided Design) software, designers can create detailed 3D models that will guide the manufacturing process.
2. Material Selection
Once the design is finalized, selecting the right material for the mold is critical. Common materials used include:
- Steel: Known for its durability and strength, making it ideal for long-run molds.
- Aluminum: Lightweight and cost-effective, perfect for low-volume production.
- Copper: Offers excellent thermal conductivity, which can be advantageous in certain molding processes.
3. Prototype Development
Before mass production, creating a prototype mold can be beneficial. This prototype allows manufacturers to test the design and functionality before committing to full-scale production. Rapid prototyping techniques, such as 3D printing, can significantly accelerate this phase, saving time and money.
4. Machining and Fabrication
After successful validation of the prototype, the actual mold fabrication process begins. This phase involves various machining processes:
- Milling: The mold is cut into shape using CNC (Computer Numerical Control) machines for high precision.
- EDM (Electrical Discharge Machining): This technique helps in achieving complex geometries that are otherwise too complicated to cut.
- Polishing: The surfaces of the mold are polished to reduce friction and improve the surface finish of the finished parts.
5. Assembly and Testing
After the components of the mold are machined and polished, they are assembled. The mold is then tested to ensure it forms the desired parts accurately and efficiently. Any adjustments or modifications are made at this stage to refine the mold’s performance.
The Benefits of Investing in High-Quality Mold Tooling
Investing in high-quality mold tooling offers numerous benefits that can directly enhance the manufacturing process:
1. Improved Quality Control
High-quality molds ensure greater consistency in the products manufactured. This reliability contributes to better adherence to quality control protocols and results in fewer defects.
2. Scalability
As businesses grow, the demand for production often increases. Well-designed mold tooling allows for scalability, meaning that as demand rises, production can keep pace without compromising on quality.
3. Enhanced Production Speeds
Efficient mold tooling can lead to faster cycle times in the production process. This efficiency allows manufacturers to meet tighter deadlines and fulfill orders more effectively.
Future Trends in Mold Tooling
The field of mold tooling is continuously evolving, driven by technological advancements and market demands. Here are some emerging trends that metal fabricators should keep an eye on:
1. Greater Use of Automation
Automation is transforming how mold tooling is designed and produced. Automated processes reduce human error, cut down labor costs, and increase overall efficiency. Companies that adopt automation can focus more on strategic decision-making than on repetitive tasks.
2. Advances in Materials Technology
Innovations in materials science are leading to better mold materials that enhance durability and performance. These advancements enable the production of more complex and intricate designs while maintaining performance standards.
3. Sustainability Practices
As industries focus more on sustainability, mold tooling companies are developing practices that reduce waste and energy consumption. Eco-friendly materials and processes are becoming a priority to minimize the environmental impact of manufacturing.
Conclusion
In conclusion, mold tooling is an indispensable aspect of the metal fabrication industry. By understanding the processes involved, the significance of high-quality tooling, and the latest trends, metal fabricators can position themselves advantageously in a competitive market. Investing in superior mold tooling not only enhances operational efficiency but also paves the way for innovative manufacturing solutions that can drive growth and success in the industry. As you explore options for your manufacturing needs, consider the profound impact that effective mold tooling can have on your operations and overall business strategy.
For further insights and advanced solutions in mold tooling, visit deepmould.net.