Understanding Tooling Molds: A Comprehensive Guide for Metal Fabricators
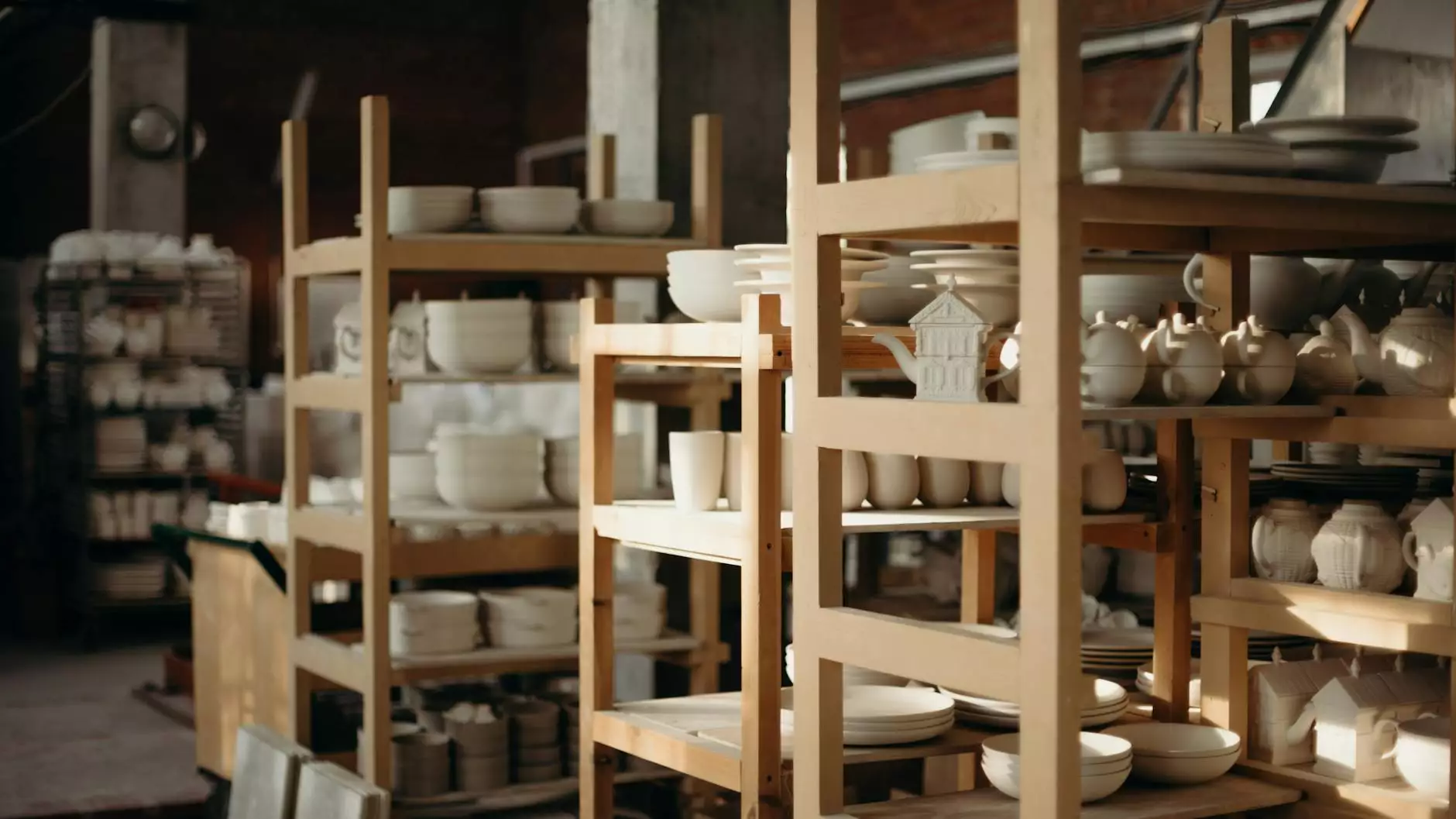
Tooling molds play a crucial role in the manufacturing and fabrication industries, especially for metal fabricators. They serve as the foundation for producing various components with precision, accuracy, and efficiency. In this guide, we will explore the various aspects of tooling molds, their significance, types, and applications, providing you with a detailed understanding of how they impact the business of metal fabrication.
The Importance of Tooling Molds in Metal Fabrication
Metal fabrication involves the process of constructing machines and structures from raw metal materials. Tooling molds are essential in this process as they facilitate the creation of highly intricate shapes and designs. By using tooling molds, manufacturers can:
- Enhance product consistency and quality
- Reduce production time and costs
- Allow for efficient mass production
- Ensure precise measurements and specifications
What is a Tooling Mold?
A tooling mold is a hollow form used to shape materials such as metal during the fabrication process. Typically made from high-strength materials, these molds act as both a template and a structure in which raw materials are inserted and shaped under pressure. Tooling molds are utilized in various production methods, including:
- Injection Molding
- Blow Molding
- Compression Molding
- 3D Printing
The Different Types of Tooling Molds
Understanding the different types of tooling molds is crucial for metal fabricators. Each type is designed for specific applications and materials. Here are the main types:
1. Injection Molds
Injection molds are commonly used for shaping thermoplastics and thermosetting plastics. They work by injecting molten material into the mold cavity and allowing it to cool and solidify. The precision of this process makes it ideal for large-scale production runs. Key benefits include:
- High efficiency and production speed
- Ability to create complex geometries
- Smooth surface finishes
2. Blow Molds
Blow molding is primarily used to create hollow plastic parts. The process involves inflating heated plastic inside a mold to form various shapes such as bottles or containers. This technique is advantageous for:
- Creating lightweight and durable products
- Reducing waste material
- Allowing for rapid production cycles
3. Compression Molds
Compression molds are used in processes where materials are placed in an open mold cavity and then compressed with a top material. This method is efficient for producing larger parts and is often utilized in industries such as automotive and aerospace. The advantages of compression molding include:
- Low tooling costs
- Versatile processing for various forms of materials
- High production flexibility
4. 3D Printed Molds
Advancements in technology have led to the development of 3D printed molds, which allow for rapid prototyping and customized mold designs. This innovative approach provides metal fabricators with more creative freedom, accommodating unique project requirements:
- Shortened lead times for mold production
- Ability to create intricate designs
- Cost-effectiveness for small production runs
Applications of Tooling Molds
Tooling molds find applications across a variety of industries, making them indispensable in the world of manufacturing. Here are some of the major fields where tooling molds are crucial:
1. Automotive Industry
The automotive industry relies heavily on tooling molds for producing parts such as dashboards, door panels, and engine components. These manufacturers require high precision and superior finish, all of which can be achieved through well-designed tooling molds.
2. Consumer Goods
Consumer products such as kitchenware, electronic housings, and toys are produced using various types of tooling molds. Fabricators can create aesthetically pleasing and functional products at scale, meeting consumer demand efficiently.
3. Aerospace and Defense
In aerospace and defense, tooling molds must meet strict regulations and withstand extreme operational conditions. High-quality molds are essential in crafting lightweight and durable parts, ultimately contributing to overall safety and performance.
4. Medical Devices
The medical industry also utilizes tooling molds for creating precision components utilized in medical devices and equipment. These products often require biocompatible materials and undergo rigorous testing, necessitating the use of reliable molds.
Benefits of Using Tooling Molds in Business
Investing in quality tooling molds can provide metal fabricators with numerous advantages that translate to business benefits, including:
1. Cost Efficiency
Although the initial investment in tooling mold design and manufacturing can be high, the long-term savings realized from efficient production processes, reduced waste, and fewer defects often outweigh these costs.
2. Increased Production Rates
With optimized tooling molds, metal fabricators can significantly increase their production rates. Faster cycle times and the ability to produce numerous parts simultaneously lead to greater output and revenue.
3. Enhanced Product Quality
The precision associated with tooling molds ensures that every part produced meets stringent quality standards. This reliability builds customer trust and enhances brand reputation.
4. Innovation Opportunities
Tooling molds allow for seamless integration of innovative designs and features, giving businesses the opportunity to differentiate their products from competitors and cater to changing market demands.
Conclusion
In conclusion, tooling molds serve as a cornerstone in the metal fabrication industry. They not only enhance the efficiency and cost-effectiveness of production but also ensure product quality and innovation. As the landscape of manufacturing continues to evolve, prioritizing the development and utilization of advanced tooling molds will be pivotal for businesses like Deep Mould. By understanding the benefits and applications of these molds, metal fabricators can leverage their capabilities to foster growth and maintain a competitive edge in the market.
Investing in quality tooling molds is not merely an operational necessity; it is a strategic decision that can enhance a company's overall performance and impact in the metal fabrication industry.